Selected Projects
See my publications page for articles related to each project.
Click images
for a description of the image.
Table of Contents
Podracer in-space refueling shuttle demo mission
The mission focuses on reducing the risk associated with in-space refueling components while enabling collaboration between companies in developing a sustainable in-space economy. I designed the mission while at Orbit Fab, and managed the mission objectives and payload during the lean and rapid 9-month program. Acting as a refueling satellite prototype, the mission paves the way to preventing satellites from becoming space debris, contributing to responsible disposal practices. Upon completion of its primary mission objectives, the Podracer spacecraft may engage in joint operations with partner spacecraft, supporting a circular economy in space.
Tenzing in-space refueling depot demo mission
This mission, named Tanker-001 Tenzing after one of the first two men to summit Mt. Everest, was deployed by Orbit Fab as the world’s first commercial satellite refueling depot in orbit. It carries high-test peroxide monopropellant and is currently orbiting in low-Earth orbit. I was a member of the team that performed the propellant compatibility and conditioning tests for the satellite propellant tank, and performed final assembly of the satellite prior to its delivery to the launch pad.
Space-resource-derived propellant
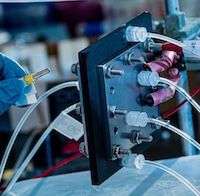
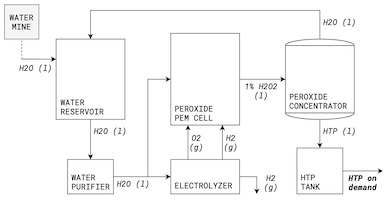
I created a system which turns water into high concentration hydrogen peroxide propellant. I designed this system, which currently has a patent pending, while at Orbit Fab. This was motivated by a need for a storable propellant that can be produced in space for use in space. Transporting propellant from the surface of Earth into orbit or to the Moon is expensive, and unsustainable long term. Hydrolox propellant, which has been proposed for production on the Moon, is very challenging to handle and store. Hydrogen peroxide is a more storable alternative, and as far as I am aware this is the first and only system which could be capable of producing it in space from locally available water. Importantly, the system is gravity-independent and does not require an atmosphere to operate, making it possible to use in orbit or on the surface of an asteroid or comet.
BioArchos decentralized carbon capture
I cofounded BioArchos with the goal of creating a decentralized system capable of permanently sequestering carbon dioxide from the atmosphere in an ecologically sustainable way. The company's hardware aimed to reduce the carbon footprint of a large office building by the equivalent of 150,000 trees, similar to placing hundreds of acres of forest in the heart of a city, cutting 20% of a building’s HVAC energy bills and improving the air quality inside. We created a bioreactor prototype of the system which used Chlorella vulgaris algae to capture and store carbon dioxide. We raised funding from the Washington Research Foundation, participated in the NSF I-Corps program, and ranked highly in two business competitions.
International Space Station life support system
I was a member of the small team at Honeywell Defense & Space designing a replacement for the aging International Space Station (ISS) Carbon Dioxide Removal Assembly as a summer intern. The Honeywell system uses a continuously circulating ionic liquid to capture carbon dioxide from the cabin air and transport it to the Sabatier reactor where it is converted into methane and disposed of. One of the issues with the current ISS system is that it maintains carbon dioxide in the atmosphere of the ISS at elevated levels which cause headaches, fatigue, and decreases in cognitive ability among the astronauts. The new system is far more capable, and also inspired me to found BioArchos, which addressed the same problem of too-high carbon dioxide levels in office buildings and schools on Earth.
Asteroid impactor sample return
I was a member of the Kinematics and Impacts Lab run by P.I. Robert Winglee, whose goal was to develop the solar system’s lowest-cost sample return vehicles. We were focused on sample return from asteroids, comets, and icy moons. I developed a mechanical sample retrieval system (dubbed Space Bear Trap), and was involved in test launches of the supersonic impactor vehicle in the wilderness of Eastern Washington.
Assistive fingertip sensors
See a video of the assistive feeding robot
in action!
I was a member of the Personal Robotics Lab run by P.I. Siddhartha Srinivasa. I worked in
the lab as a hardware engineer, designing and manufacturing soft force-sensitive robotic fingers. I collaborated
with the team of software engineers and researchers at various universities to miniaturize an existing robotic
finger, in order to use it for robot-assisted feeding for people who are unable to feed themselves.